As vital as it is for a home’s indoor environment to be human-friendly, it is even more crucial for any industry, whether in the chemical, processing, manufacturing, power generation, textile, or pharmaceutical sectors, for its environment and temperature to be human-friendly.
Visit TameerEasy Store to Purchase Quality Construction Items
Although installing commercial & Domestic cooling and heating system in industrial settings can be difficult, no one ever tells you about it. What kind of installing commercial HVAC cooling and heating system, how to install it, and which technique is best and most common place for it should be implemented in an industrial or commercial HVAC setting? In this article, we’ll strive to answer all of these queries.
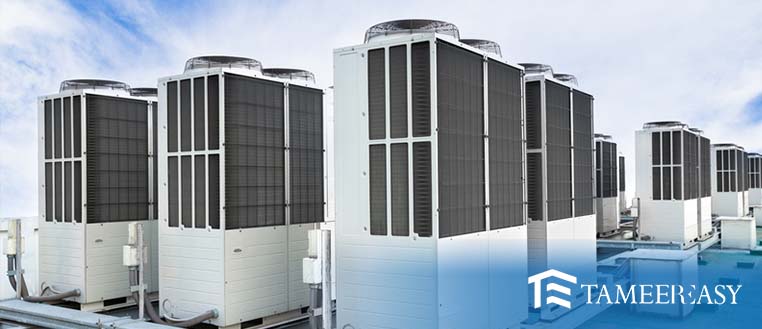
Different Commercial HVAC System Types
Understanding the many types and larger components of an industrial or commercial-level system is crucial for effective system installation that considers your preferences.
Two types of Commercial HVAC systems are employed at the industrial level:
Air-Cooled
Compressor, pressure gauge, condenser, shut-off valve, filter, expansion valve, water in and water out pipes for the evaporator, drain, drip pan, and high and low-pressure protection condenser fans are among the parts of air-cooled systems.
Water-Cooled
These elements are also present in water-cooled systems, but a cooling tower, chillers, pumps, and a liquid cooler are also present.
Heating and Cooling System (H&C) Components
Typically, an H&C system consists of the following parts:
- Air Separators
- A Compressor
- A Chiller
- A Command Structure
Cooling towers, ventilation fans, heating boilers and furnaces, air handling units, fan coil units, ducts, and pipes are all included if the system is water-cooled. Additionally, copper pipes and ducts are added if the system is air-cooled.
Which is the Best Type? Either Water- or Air-cooled
We will now examine its cooling capacity and price for you so that you can determine which system is superior based on the best testing standards.
If we start with the water-cooled system, it has a higher cooling capacity, is more energy-efficient, and can operate for a very long time due to the longevity of the equipment. However, compared to air-cooled, its capital cost is higher because it also includes hiring the contractor and the cooling tower.
Compared to other cooling systems, air-cooled has lower capital and maintenance costs. Its performance at freezing temperatures will be good, and it is a bundled system that is simple to install and design.
However, it consumes more power, has a higher running cost, and is less energy-efficient. Another disadvantage is that it is exposed to the elements outside, which shortens its lifespan. In contrast, water-cooled equipment that is located indoors will have a longer lifespan because the weather will not have an impact on it.
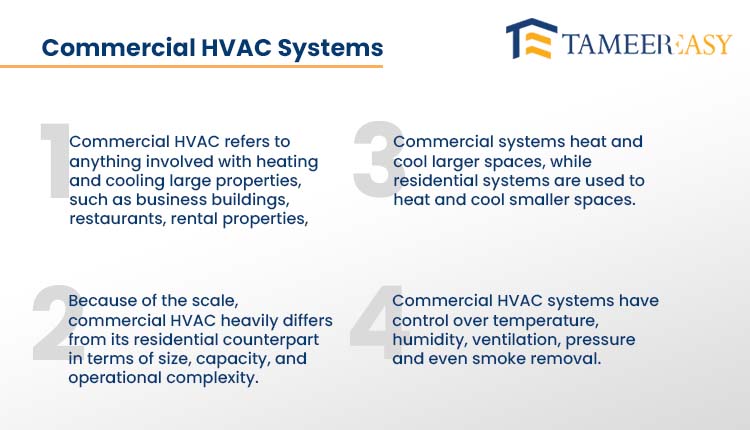
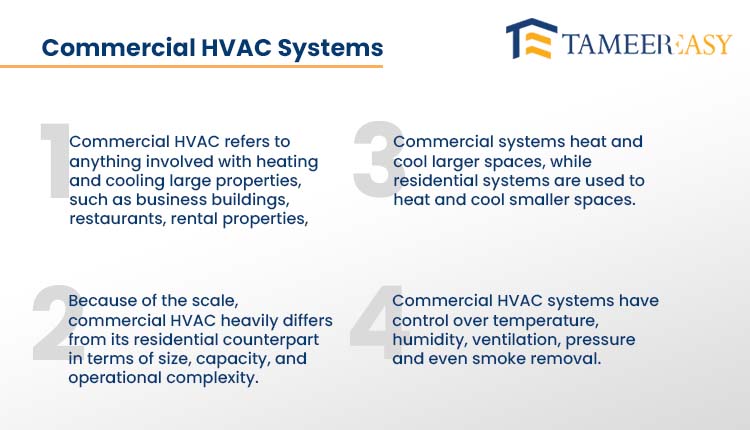
Pipe Selection for Heating and Cooling Systems
One thing to keep in mind is that since we are discussing an industrial-scale, commercial HVAC heating and cooling system, their pipes will also be unique. The insulation surrounding the pipes is also very significant.
We’ll start by explaining that we employ seamless steel from MS Schedule 40. After that, insulation is put on the four to five types of pipes used. Additionally, copper pipes are an option.
These include closed-cell insulation, polyurethane, rock wool/fibreglass, polyethene, polythene, polythene insulation, and fibreglass and polyethene insulation.
One other thing to note is that these four to five different types of insulation will be used for duct insulation and pipes.
Choosing the Insulation’s Thickness
- The environmental conditions in the location determine the insulation’s thickness. Glass wool insulation typically has a density of 60 plus or less and measures between half an inch and one inch in thickness.
- We can install cladding to cover the insulation if it is outside, such as on a rooftop. This holds for places like basements where a lot of moisture is present. As a result, the insulation’s density and thickness are considered.
- A BMS system, coupled with sensors, gauges, pressure gauges, temperature gauges, flow metres, etc., can be used to monitor this system. All of these elements are necessary for effective monitoring.
The Installation of the Heating and Cooling Systems
- The first thing to remember is that the commercial heating and cooling system is complicated and needs to be installed by a skilled industrial contractor with knowledge of energy efficiency to be built efficiently, promptly, and affordably.
- We must carefully install everything because cooling towers, chillers, ducting, and piping are all involved in the system’s installation. Additionally, a control system is also necessary.
- It must be adequately insulated to build ductwork for its quality and design and to prevent condensation—which is also required for our chilled water lines.
- Installing our cooling tower is a crucial stage because it will be outside. Then, we must remember that while the ductwork is installed, our pipes, cable trays, power cables, and control systems will also be installed. While a result, we must maintain everything correctly to prevent any mishaps.
- An experienced industrial contractor with the right skills can complete all of this.
- Now that the ducting is in place, we must check for leaks, hydro-test the pipes and install the power cable within cable trays to ensure no issues.
- One additional item to note is that a good water treatment programme should be in place to ensure that the water used in the cooling tower is adequately treated to prevent any scaling, corrosion, or fouling issues.
The Value of Chillers and Their Purpose
The refrigeration cycle shares a fundamental feature with chillers. This means that if it contains a vapour compression cycle, it will also have a vaporizer, condenser, compressor, and any throttling or expansion fins that may be present.
These are the elements that make up a chiller. There are now two different types of chillers; one relies on a cycle that compresses and absorbs vapours, and the other does the opposite. Another name for the vapour compressor is an electric chiller. The different type, which can be thought of as a vapour absorption or generator, is powered by diesel or natural gas.
As its name implies, the vapour absorption cycle is a fire-generation process. Reciprocal, screw, scroll, and centrifugal compressors are used in vapour compression chillers. Additionally, single and double-effect chillers are utilized in vapour absorption chillers.
There are several fundamental chiller types in addition to these two chillers. It also includes single-stage, direct or indirect fired, double-stage, and multi-stage systems. This answers the second part of your inquiry about how it operates. Chillers operate according to the refrigeration cycle, whether it is a vapour compression cycle or a vapour absorption cycle. If anything relies on refrigeration, then refrigeration is used to chill it.
Primary and Secondary Pumps
Let us add one more item to this: if your project is quite massive, you can use a chiller, a machine frequently used in businesses. We need to employ primary and secondary pumps in this situation. The primary pump keeps the chiller’s flow and minimum capacitance stable.
The pressure and flow rates of the two pumps can be used to distinguish them. Because the primary pump has a minimum capacitance that must be maintained with the chiller, its flow rate is constant. In contrast, the flow rate inside the secondary pump is variable. The secondary pump handles the building’s load; therefore, it fluctuates. As a result, its load also changes.
The pumps will raise the flow if consumer consumption rises, which is the reason. The pump’s speed will be reduced if it falls. Because it simply maintains the chiller’s discharge, the primary pump’s speed is constant, whereas the secondary pump’s rate varies.
Ducts Usage in Chillers
- Instead of using straight-size ducts, duct gauges that have been validated to meet the needs of each project’s design are employed.
- The gauges that we typically employ are 16, 18, 20, 22, 24, and 26.
- We occasionally also need to utilize canvas cloth. We will insulate it and leave it where the insulation will have sealing.
- Because it depends on the conditions there and the intended users, cladding can also be used.
Commercial Level Variable Refrigerant Flow (VRF)
The VRF system is very useful in homes and other household settings. Think of it as a substitute for our water-cooled system. Additionally, it has indoor and outdoor units. We design it by the project’s load capacity.
The load is connected to indoor units in the same area. This connection makes use of appropriate copper piping. Depending on their capacity, indoor units are connected to outdoor units in a certain number.
We gain from this because we can choose exactly which area to cool. For instance, we can cool three out of 10 locations. So, VRF is also applicable in the industrial setting.
Important Safety Reminders
As you know, we will be installing this system in the industry, so passing through valves will be there, whether from ducts, MS steel pipes, copper pipes, or other types of pipes.
We will apply fire sealants on the ducts, table trays, or pipes above it if there are any fire zone regions there, especially in electrical rooms, IT rooms, or our pump rooms, which are energy centres, to keep them safe from potential fire threats.
Final Remarks
Now that you’ve learned more about the industrial heating and cooling system, you undoubtedly know how to install it in your industrial or commercial HVAC building. However, visit our website at tameereasy if you still need more advice or have any questions.